Industrial cleaning plays a crucial role in maintaining the efficiency and safety of industrial facilities. From manual to chemical cleaning methods, each type serves a specific purpose in keeping work environments clean and operational.
We will explore the importance of industrial cleaning, the different types of cleaning processes, the steps involved, and the safety measures to ensure a smooth and hazard-free operation.
Let’s delve into the world of industrial cleaning and discover the key factors that make it essential for businesses.
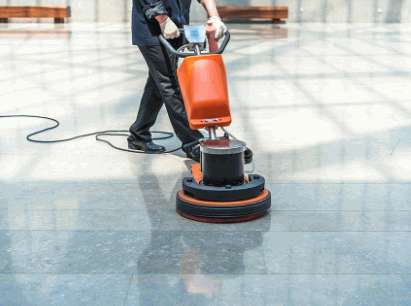
What Is Industrial Cleaning?
Industrial cleaning is the process of maintaining cleanliness in industrial facilities such as power plants, manufacturing facilities, warehouses, and factories to ensure a safe and healthy working environment.
This process involves the removal of dirt, debris, contaminants, and hazardous substances that accumulate in these industrial settings.
Industrial cleaning plays a crucial role in preventing accidents, improving operational efficiency, and extending the lifespan of equipment and machinery. It is essential for compliance with health and safety regulations, environmental standards, and quality control measures. Some specialized areas that require professional industrial cleaning services include confined spaces, high-level structures, and equipment with intricate parts that demand thorough and precise cleaning procedures.
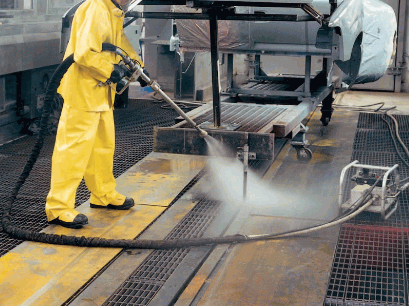
Why Is Industrial Cleaning Important?
Industrial cleaning is crucial for maintaining the operational efficiency and safety of industrial facilities. Professional industrial cleaning services ensure that the facilities adhere to the standards set by regulatory bodies like the Environmental Protection Agency (EPA) and the Occupational Safety and Health Administration (OSHA).
Complying with the guidelines set by these regulatory bodies not only helps prevent accidents and injuries but also contributes to the overall sustainability of the industrial sector. It is essential for industrial cleaning companies to stay updated with the latest regulations and requirements to provide effective services that meet industry standards.
The thorough cleaning of equipment and machinery not only extends their lifespan but also enhances their performance, leading to increased productivity and reduced downtime. By investing in regular industrial cleaning services, businesses can ensure a safe, efficient, and compliant working environment.
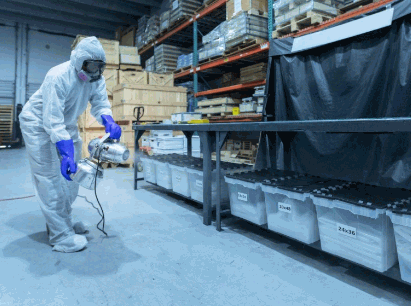
What Are The Different Types Of Industrial Cleaning?
Industrial cleaning encompasses various methods tailored to different requirements, including manual cleaning, mechanical cleaning, chemical cleaning, high-pressure cleaning, and vacuum cleaning.
Each method has its own advantages and applications in the industrial sector.
- Manual cleaning, for instance, offers precision in reaching intricate areas and removing specific contaminants efficiently.
- Mechanical cleaning, on the other hand, provides a more automated and consistent approach, ideal for large-scale operations.
- Chemical cleaning involves the use of specialized agents to dissolve tough residues and sanitize surfaces effectively.
- High-pressure cleaning is highly effective for removing stubborn dirt and coatings.
- Vacuum cleaning, renowned for its ability to remove dust and particulates, plays a crucial role in maintaining cleanliness and hygiene standards in industrial environments.
Manual Cleaning
Manual cleaning involves physical labor and the use of cleaning tools to remove dirt, debris, and contaminants from industrial surfaces.
In industrial settings, manual cleaning plays a crucial role in maintaining hygiene and ensuring safety standards. Workers typically use tools such as scrub brushes, mops, squeegees, and scrapers to effectively eliminate grime and substances that are hard to remove with automated methods. This hands-on approach allows for meticulous attention to detail, especially in hard-to-reach areas or delicate equipment that cannot withstand harsh cleaning agents. Manual cleaning is particularly effective in spaces where precision and thoroughness are paramount, such as food processing facilities, healthcare environments, and laboratories.
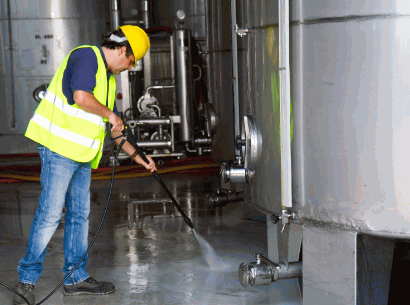
Mechanical Cleaning
Mechanical cleaning utilizes machinery and equipment to automate the cleaning process in industrial facilities, enhancing efficiency and reaching inaccessible areas.
Specialized equipment such as high-pressure washers, scrubbers, and sweepers play a crucial role in tackling tough industrial dirt and grime. These tools are designed to efficiently remove contaminants from various surfaces, including floors, walls, and machinery. Robots equipped with advanced sensors and AI technology are being increasingly employed to handle intricate cleaning tasks and navigate complex industrial environments.
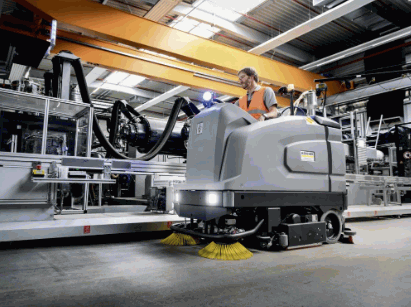
Chemical Cleaning
Chemical cleaning involves the use of solvents, detergents, and cleansing agents to dissolve and remove contaminants from industrial equipment and surfaces.
These cleaning agents work by breaking down stubborn dirt, grease, and other substances that accumulate over time, allowing for thorough cleaning of machinery, tanks, pipelines, and other industrial components. Chemical cleaning is a highly effective method for restoring equipment to optimal operational conditions, improving efficiency, and prolonging the lifespan of industrial assets. Various types of chemicals such as acids, alkalis, and solvents are used depending on the nature of the contaminants and the material of the equipment being cleaned.
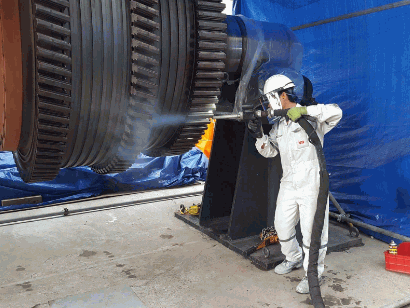
High-Pressure Cleaning
High-pressure cleaning utilizes water jets at high pressure to dislodge dirt, grime, and residue from industrial surfaces, ensuring thorough cleaning and restoration.
One of the key advantages of high-pressure cleaning is its ability to tackle tough stains and deposits that traditional cleaning methods struggle to remove. The sheer force of the water jets can penetrate deep into crevices, effectively eliminating built-up grime.
The use of high-pressure water jets reduces the need for harsh chemical cleaners, making it an environmentally friendly cleaning solution for industrial facilities. This not only enhances safety for workers by minimizing exposure to harmful chemicals but also promotes sustainability.
Discover more: Does Power Washing Remove Wood Stain
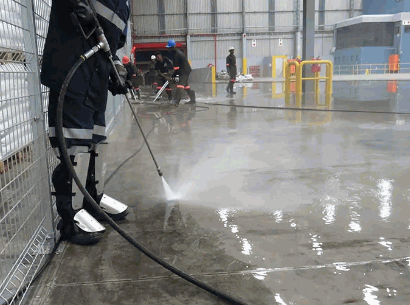
Vacuum Cleaning
Vacuum cleaning involves the use of suction devices to remove dust, particles, and contaminants from hard-to-reach areas in industrial facilities, enhancing cleanliness and air quality.
Industrial vacuum systems vary in size and complexity, ranging from portable units for spot cleaning to centralized systems that service an entire facility. These systems utilize high-powered motors to generate significant suction force, capable of capturing both solid debris and liquid spills effectively. Common applications include cleaning production lines, machinery, floors, and overhead structures. By maintaining a clean environment, businesses can reduce the risk of equipment malfunctions, improve worker safety, and comply with regulatory standards for cleanliness and hygiene.
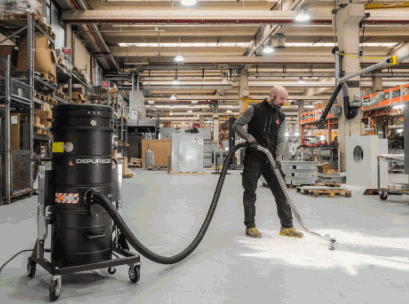
What Are The Steps Involved in Industrial Cleaning?
Industrial cleaning encompasses several key steps, including assessment and planning, preparation, the cleaning process, and inspection, which are crucial for maintaining cleanliness and safety standards in industrial facilities.
Assessment and planning are the initial stages where experts evaluate the facility’s unique needs and create a tailored cleaning strategy.
Proper preparation involves securing necessary equipment, and chemicals, and ensuring the safety of personnel and the environment before commencing the cleaning process.
The heart of industrial cleaning lies in the meticulous cleaning process itself, where trained professionals execute the plan with precision.
A critical step that follows is the inspection phase, where the effectiveness of the cleaning is assessed, ensuring compliance with regulations and standards for a truly spotless outcome.
Assessment And Planning
The initial phase of industrial cleaning involves assessing the facility’s cleaning needs, identifying potential hazards, and devising a strategic cleaning plan to address specific requirements.
During this crucial assessment and planning stage, it is essential to conduct a meticulous evaluation of the entire site to determine the extent of cleaning required. This involves inspecting all areas, from production floors to office spaces, to understand the diverse cleaning needs arising from different environments within the facility. By conducting a comprehensive risk assessment, potential safety hazards such as slippery surfaces or chemical spills can be identified and mitigated effectively.
Preparation
Preparation for industrial cleaning includes securing the necessary equipment, ensuring safety protocols are in place, and scheduling the cleaning activities to minimize disruptions to regular operations.
Having the appropriate tools for the job is crucial in industrial cleaning. This involves checking that vacuum cleaners, pressure washers, scrubbers, and cleaning solutions are all in proper working order. Equipment readiness can make a significant difference in the effectiveness and efficiency of the cleaning process.
Safety measures play a vital role in protecting workers and preventing accidents. Ahead of commencing any cleaning tasks, it is essential to provide proper training on handling chemicals, wearing protective gear, and following established safety guidelines to reduce risks.
Additionally, logistical planning ensures that the cleaning crew knows which areas need attention and the sequence in which tasks should be carried out. This minimizes confusion and streamlines the cleaning process, leading to better results in a shorter timeframe.
Cleaning Process
The core stage of industrial cleaning involves the systematic execution of cleaning tasks using the selected methods and technologies to achieve optimal cleanliness and hygiene standards.
Upon determining the cleaning requirements, industrial facilities typically begin by clearing the area of any equipment and materials to be cleaned. Advanced equipment, such as high-pressure washers and specialized cleaning solutions, are then utilized to remove tough stains and residues. Additionally, industrial cleaning may involve the use of scrubbing machines for large surface areas and vacuum units to address debris. Careful inspection is crucial to ensure thoroughness, followed by disinfection procedures to maintain sanitized conditions.
Inspection And Quality Control
The final phase of industrial cleaning includes a thorough inspection, quality control checks, and validation of cleaning outcomes to ensure compliance with industry standards and client requirements.
During this phase, meticulous scrutiny is applied to various aspects of the cleaning process. This involves inspecting surfaces for any remaining contaminants, checking the effectiveness of cleaning solutions used, and examining equipment for proper functionality. Quality control measures such as spot-checking, sampling, and testing are implemented to verify the cleanliness and sanitation levels achieved post-cleaning. Any identified deficiencies or deviations from standards are promptly addressed to maintain high-quality assurance standards. By conducting these meticulous inspections and quality control checks, industrial cleaning services can guarantee optimal results and client satisfaction.
What Are The Safety Measures For Industrial Cleaning?
Ensuring safety during industrial cleaning operations is paramount, necessitating the use of Personal Protective Equipment (PPE), comprehensive training programs, hazard identification protocols, and emergency response plans to mitigate risks and ensure worker well-being.
One of the crucial aspects of industrial cleaning safety is the meticulous assessment of potential hazards that workers may encounter in their tasks. This involves conducting thorough evaluations of the work environment to proactively identify risks and implement control measures. By adopting a systematic approach to hazard assessment, organizations can preemptively address dangers such as chemical exposure, falls, confined spaces, and equipment malfunctions.
Personal Protective Equipment (PPE)
Personal Protective Equipment (PPE) such as gloves, goggles, masks, and protective clothing is essential for safeguarding workers from exposure to hazardous materials and maintaining their well-being during industrial cleaning tasks.
These PPE items create a crucial barrier between the workers and potential risks, preventing injuries, illnesses, or accidents that can occur during cleaning operations. Gloves shield hands from chemical splashes or cuts, while goggles safeguard the eyes from harmful fumes or particles. Masks play a vital role in filtering out airborne contaminants, and protective clothing covers the body, reducing skin contact with harmful substances.
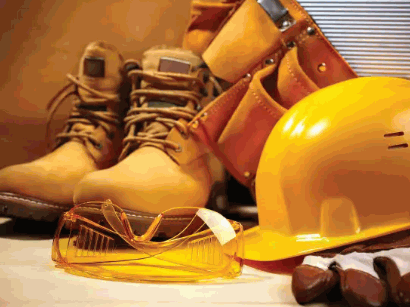
Proper Training And Certification
Comprehensive training programs and certifications are vital to equip industrial cleaning professionals with the necessary skills, knowledge, and safety protocols to perform cleaning tasks effectively and safely.
Specialized programs cater to the unique challenges faced in industrial cleaning, such as handling hazardous materials, working with complex machinery, and adhering to strict regulations. These training initiatives go beyond basic cleaning techniques and delve into advanced methodologies that ensure not just cleanliness but also maintenance of industrial equipment. Certification serves as a testament to the individual’s proficiency and dedication to upholding industry standards. It not only boosts their credibility but also opens doors to more job opportunities within the industrial cleaning sector.
Hazard Identification And Risk Assessment
Conducting hazard identification and risk assessments before industrial cleaning activities is essential to identify potential dangers, evaluate risks, and implement preventive measures to protect workers and the environment.
Hazard identification and risk assessment involve a systematic approach to recognize, analyze, and manage risks inherent in industrial cleaning processes. By employing tools such as checklists, inspections, and job safety analysis, companies can proactively ascertain potential hazards like chemical exposure, equipment malfunctions, or slip and fall risks. This preemptive strategy not only safeguards the workforce but also ensures compliance with regulatory standards and enhances overall operational efficiency.
Emergency Response Plan
Having a well-defined emergency response plan is crucial for addressing unforeseen incidents, accidents, or spills during industrial cleaning operations, ensuring quick and effective responses to minimize harm and damage.
- An effective emergency response plan in industrial cleaning should first include a detailed assessment of potential risks and hazards specific to the cleaning processes involved, as this forms the foundation for preparedness.
- Clear communication protocols play a vital role in ensuring that all employees are aware of their roles and responsibilities in case of an emergency, with designated communication channels and procedures established.
- Mitigation strategies, such as regular training drills and investments in proper safety equipment, are essential components to proactively prevent and respond to emergencies to protect both personnel and the environment.